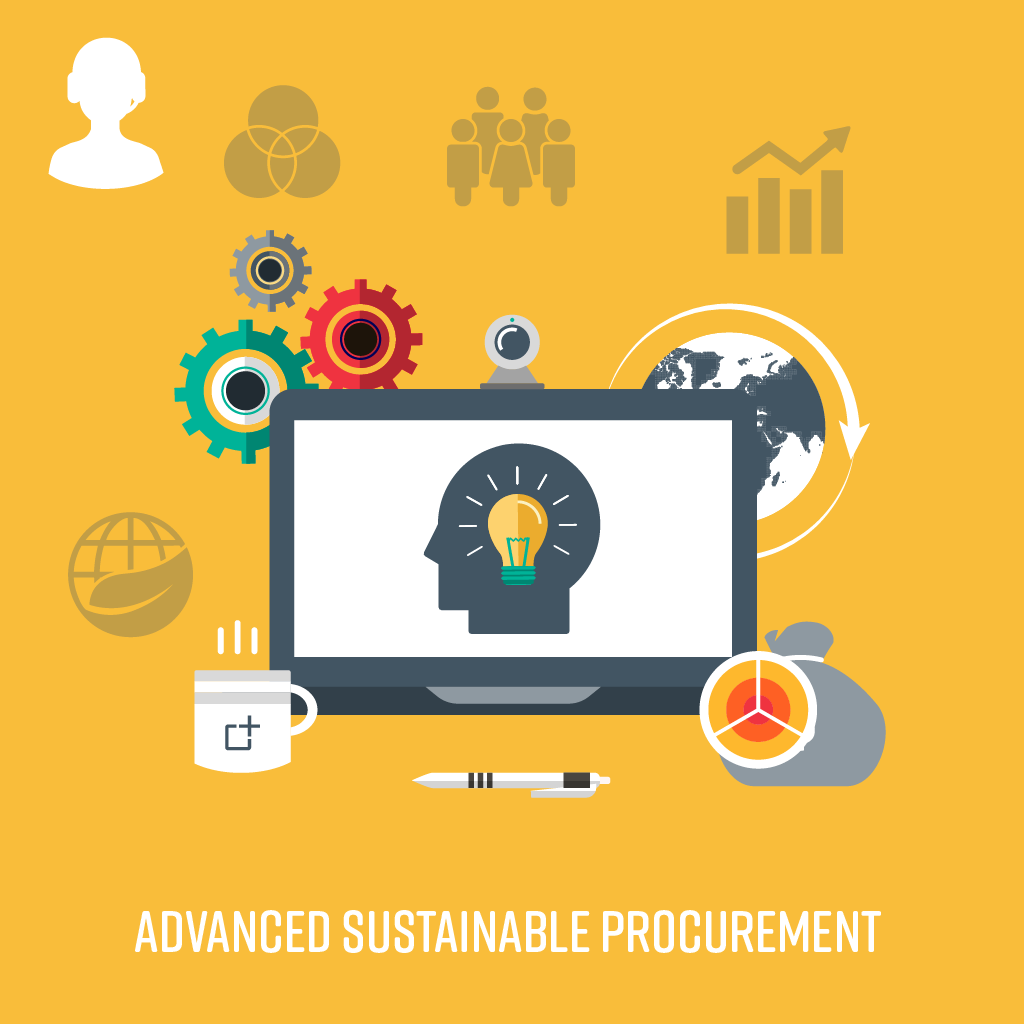
There are a wide variety of logistics jobs in Tampa. Many of these jobs are in the manufacturing, construction or healthcare industries. However you can work in the wholesale trading industry, consulting firms, or other businesses that streamline supply chains.
A degree in logistics can open up a number of career opportunities. Entry-level positions such as shipping clerks can be found with an associate degree, while more advanced jobs are available for those who hold bachelor's degrees. If you have specific goals and interests, you can specialize in a certain area of logistics.
BLS data indicates that career opportunities in logistics are growing. The BLS predicts employment growth for this profession of 5% from 2018 to 2028. It is predicted that professionals focusing on business operations will see greater job growth.
You can earn a logistics degree at a community college or a four-year university. These programs usually offer a wide range of logistics specializations. This allows you to develop more specialized skills, and make you more employable when you advance up the ladder.
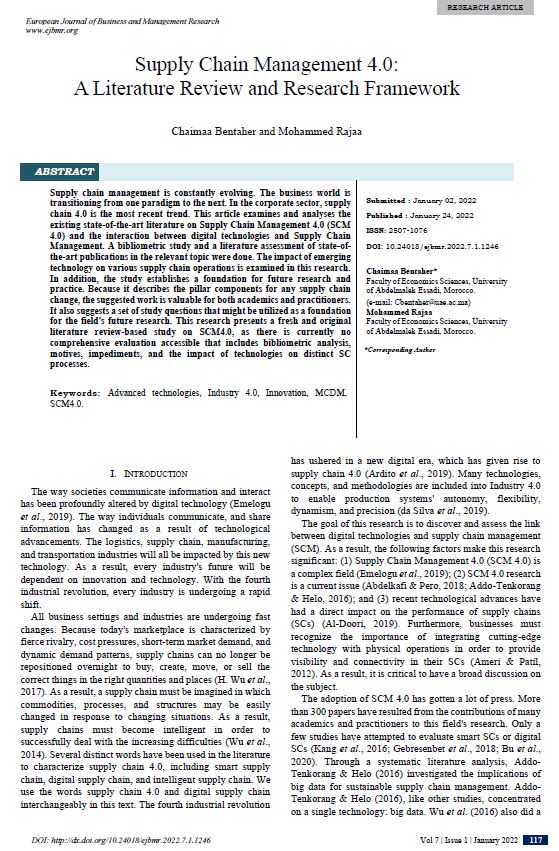
In addition to pursuing a bachelor's degree, students should consider taking part in internships and networking opportunities. These experiences will give you valuable experience in the logistics field and can help you to find your first job.
There are many job opportunities in the logistics industry. You can get a job in the logistics industry anywhere, but particularly in states with a large population and high growth, such as California and Texas. You can find jobs in many different sectors such as oil and gas, aerospace or other.
When selecting a third-party logistics company, consider the company's size and capabilities. The ideal 3PL is one that can customize a solution to fit your specific business needs. This will allow you to reduce your overall costs and increase your efficiencies.
Your business's supply chain plays a vital role in the success of its operations. You must have the right people and the right tools to ensure that your products arrive at the correct time and in perfect condition. Selecting a third-party provider of logistics that is experienced in your industry can help you improve the efficiency and effectiveness of your supply chain.
Sheer, an integrated 3PL with a Tampa base, can reduce costs and improve supply chain efficiency. We provide a range of services to our customers, including transportation, inventory management, and shipping.
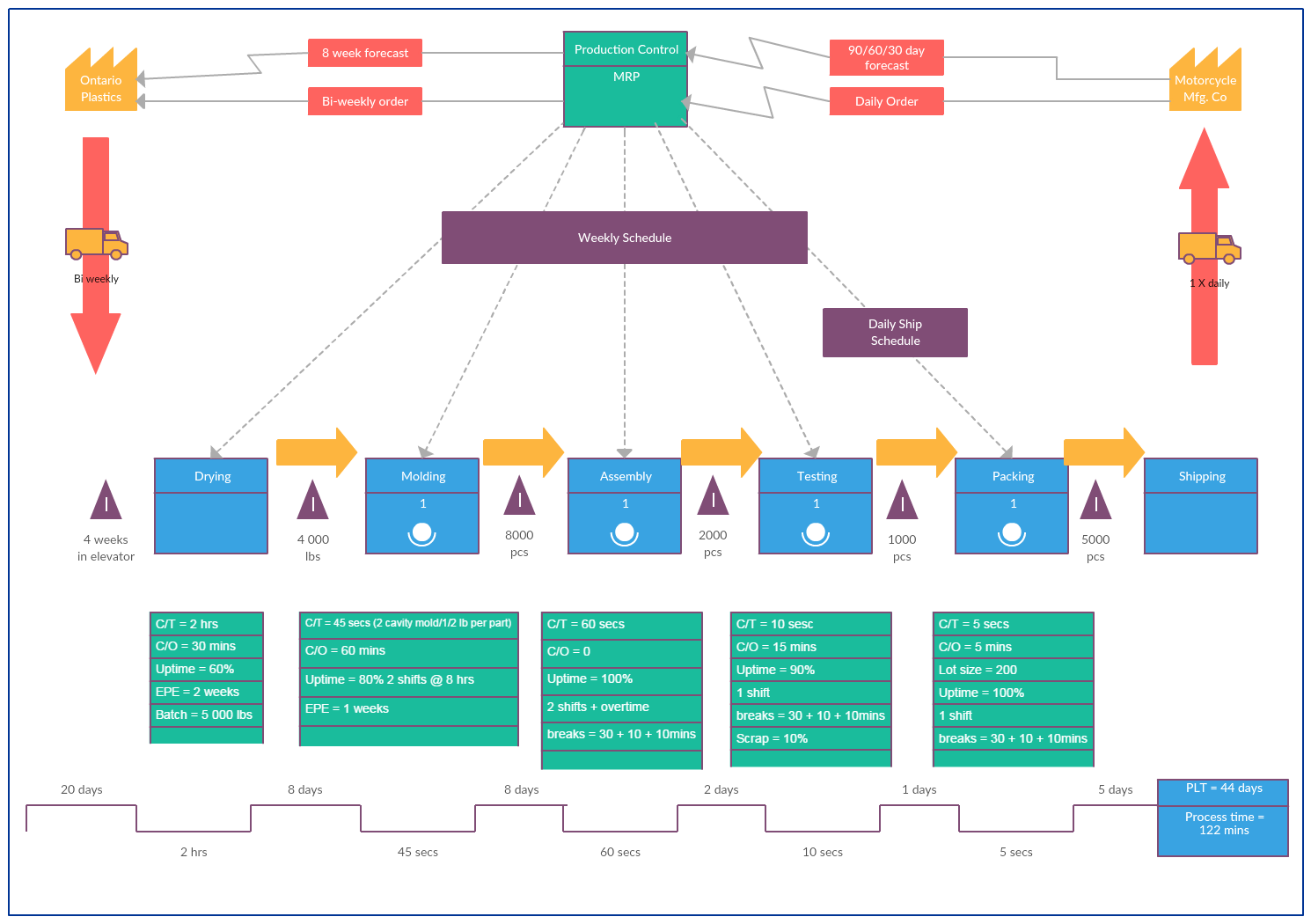
We provide you with a set of technology tools for tracking and managing your supply chains. Our cloud-based system integrates with your existing ERP, allowing you to easily monitor and control your entire business.
With Sheer, you can take advantage of our multimodal freight network and transform your supply chain from a liability to an asset. You can count on Sheer to deliver your goods safely, on time and every time.
FAQ
What are manufacturing and logistic?
Manufacturing is the process of creating goods from raw materials by using machines and processes. Logistics manages all aspects of the supply chain, including procurement, production planning and distribution, inventory control, transportation, customer service, and transport. As a broad term, manufacturing and logistics often refer to both the creation and delivery of products.
Is automation important for manufacturing?
Automation is essential for both manufacturers and service providers. They can provide services more quickly and efficiently thanks to automation. It also helps to reduce costs and improve productivity.
What is production plan?
Production Planning involves developing a plan for all aspects of the production, including scheduling, budgeting, casting, crew, location, equipment, props, etc. This document is designed to make sure everything is ready for when you're ready to shoot. It should also contain information on achieving the best results on set. This information includes locations, crew details and equipment requirements.
The first step is to outline what you want to film. You may have decided where to shoot or even specific locations you want to use. Once you have identified your locations and scenes, you can start working out which elements you require for each scene. You might decide you need a car, but not sure what make or model. If this is the case, you might start searching online for car models and then narrow your options by selecting from different makes.
Once you have found the right vehicle, you can think about adding accessories. Do you need people sitting in the front seats? Or perhaps you need someone walking around the back of the car? You may want to change the interior's color from black or white. These questions can help you decide the right look for your car. Another thing you can do is think about what type of shots are desired. Will you be filming close-ups or wide angles? Maybe the engine or steering wheel is what you are looking to film. These factors will help you determine which car style you want to film.
Once you have determined all of the above, you can move on to creating a schedule. You can create a schedule that will outline when you must start and finish your shoots. You will need to know when you have to be there, what time you have to leave and when your return home. Everyone knows exactly what they should do and when. You can also make sure to book extra staff in advance if you have to hire them. There is no point in hiring someone who won't turn up because you didn't let him know.
Also, consider how many days you will be filming your schedule. Some projects can be completed in a matter of days or weeks. Others may take several days. When creating your schedule, be aware of whether you need more shots per day. Multiple shots at the same location can increase costs and make it more difficult to complete. If you aren't sure whether you need multiple shots, it is best to take fewer photos than you would like.
Another important aspect of production planning is setting budgets. It is important to set a realistic budget so you can work within your budget. You can always lower the budget if you encounter unexpected problems. However, it is important not to overestimate the amount that you will spend. If you underestimate how much something costs, you'll have less money to pay for other items.
Production planning can be a complex process. However, once you know how everything works together it will become easier to plan future projects.
What does the term manufacturing industries mean?
Manufacturing Industries is a group of businesses that produce goods for sale. The people who buy these products are called consumers. To accomplish this goal, these companies employ a range of processes including distribution, sales, management, and production. They make goods from raw materials with machines and other equipment. This includes all types of manufactured goods, including food items, clothing, building supplies, furniture, toys, electronics, tools, machinery, vehicles, pharmaceuticals, medical devices, chemicals, and many others.
What is the difference between a production planner and a project manager?
The main difference between a production planner and a project manager is that a project manager is usually the person who plans and organizes the entire project, whereas a production planner is mainly involved in the planning stage of the project.
Statistics
- Many factories witnessed a 30% increase in output due to the shift to electric motors. (en.wikipedia.org)
- In the United States, for example, manufacturing makes up 15% of the economic output. (twi-global.com)
- You can multiply the result by 100 to get the total percent of monthly overhead. (investopedia.com)
- Job #1 is delivering the ordered product according to specifications: color, size, brand, and quantity. (netsuite.com)
- In 2021, an estimated 12.1 million Americans work in the manufacturing sector.6 (investopedia.com)
External Links
How To
How to use the Just In-Time Production Method
Just-in time (JIT), is a process that reduces costs and increases efficiency in business operations. It's the process of obtaining the right amount and timing of resources when you need them. This means that your only pay for the resources you actually use. Frederick Taylor was the first to coin this term. He developed it while working as a foreman during the early 1900s. After observing how workers were paid overtime for late work, he realized that overtime was a common practice. He then concluded that if he could ensure that workers had enough time to do their job before starting to work, this would improve productivity.
JIT is a way to plan ahead and make sure you don't waste any money. You should also look at the entire project from start to finish and make sure that you have sufficient resources available to deal with any problems that arise during the course of your project. If you expect problems to arise, you will be able to provide the necessary equipment and personnel to address them. This will prevent you from spending extra money on unnecessary things.
There are many JIT methods.
-
Demand-driven JIT: You order the parts and materials you need for your project every other day. This will enable you to keep track of how much material is left after you use it. It will also allow you to predict how long it takes to produce more.
-
Inventory-based: This type allows you to stock the materials needed for your projects ahead of time. This allows you to forecast how much you will sell.
-
Project-driven: This means that you have enough money to pay for your project. You will be able to purchase the right amount of materials if you know what you need.
-
Resource-based JIT: This type of JIT is most commonly used. This is where you assign resources based upon demand. For instance, if you have a lot of orders coming in, you'll assign more people to handle them. You'll have fewer orders if you have fewer.
-
Cost-based: This is the same as resource-based except that you don't care how many people there are but how much each one of them costs.
-
Price-based: This is a variant of cost-based. However, instead of focusing on the individual workers' costs, this looks at the total price of the company.
-
Material-based: This is very similar to cost-based but instead of looking at total costs of the company you are concerned with how many raw materials you use on an average.
-
Time-based JIT: This is another variant of resource-based JIT. Instead of focusing on how much each employee costs, you focus on how long it takes to complete the project.
-
Quality-based JIT: This is another variation of resource based JIT. Instead of thinking about the cost of each employee or the time it takes to produce something, you focus on how good your product quality.
-
Value-based JIT: One of the most recent forms of JIT. This is where you don't care about how the products perform or whether they meet customers' expectations. Instead, your goal is to add value to the market.
-
Stock-based: This stock-based method focuses on the actual quantity of products being made at any given time. This is used to increase production and minimize inventory.
-
Just-in-time planning (JIT): This is a combination JIT and supply-chain management. This refers to the scheduling of the delivery of components as soon after they are ordered. It is essential because it reduces lead-times and increases throughput.