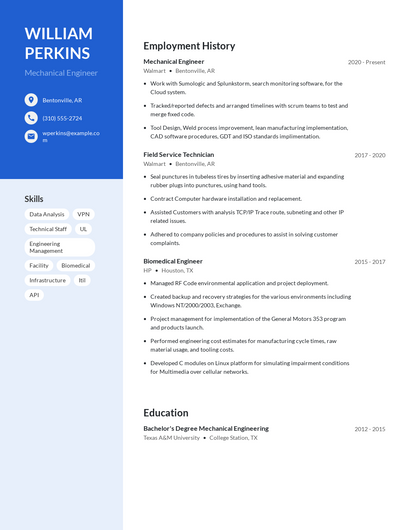
Both part-time and full time logistics jobs are available at the federal and state levels. There are many advantages to working in these jobs. They can provide stable income and great benefits. It is also possible to get work experience in the government.
For example, a Logistics Management Specialist is responsible for managing the supply chain. They oversee deliveries and manage contracts with suppliers. They work with suppliers to find supply chain deficiencies and create contingency plans. You must have excellent communication skills, great typing skills, and a good understanding of government procurement regulations.
Supply Chain Management Officers can work for the Department of Veterans Affairs or for the Department of Homeland Security. The former position requires an extensive understanding of the federal government's procurement regulations, and the latter role involves managing logistics operations and sourcing supplies. Candidates should have a bachelor's or higher degree depending on their job. In addition, applicants are expected to have a solid knowledge of the business culture and regulations of the state they're applying for. Some positions require security clearances. Candidates may need to pass a background screening.
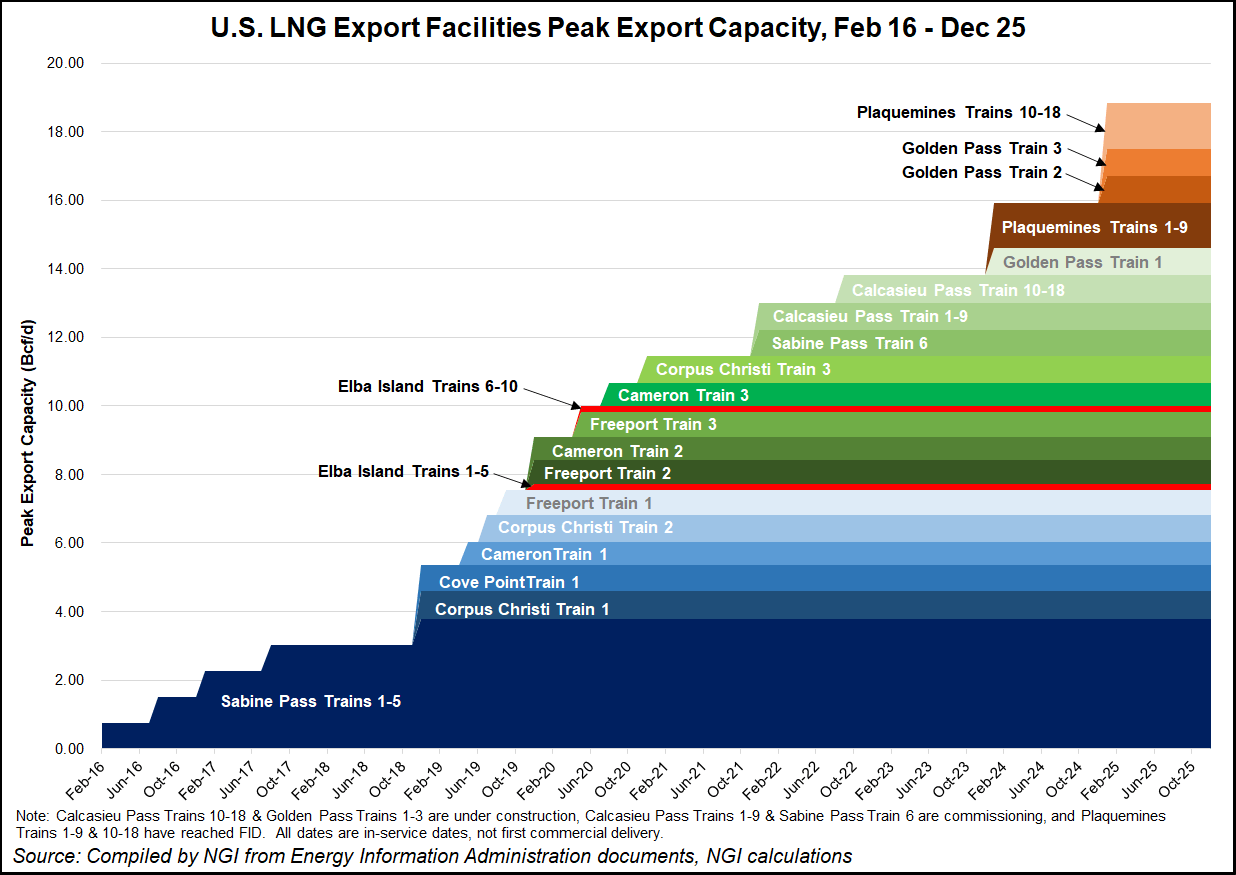
Other government logistics specialists can also be employed to deploy materials quickly after an event. A distribution role in disaster logistics is offered by the North Carolina Department of Public Safety. Candidates need to have at the least four years of relevant work experience. Because the job requires you to manage a group of people, candidates must have the ability and willingness to work under pressure.
Additionally, logistics management specialists are needed at the departmental and sub-ordinate levels. The Federal Aviation Administration's typical role for logistics specialists is very similar. The qualifications include an advanced degree, specialized knowledge in operations or project managing, and a background of logistics management.
You'll need to have the ability to handle large volumes of international travel if your goal is to become a government logistics manager. It is also necessary to have experience in managing supplier bids and procurement negotiations. Candidates will need at least two year's relevant experience.
You can also apply for a variety other supply chain management roles in the federal government. These positions are available in areas like air transport, road transportation, warehousing or distribution. Nearly 25% of these positions are offered through the federal government. Eight percent are offered via the states.
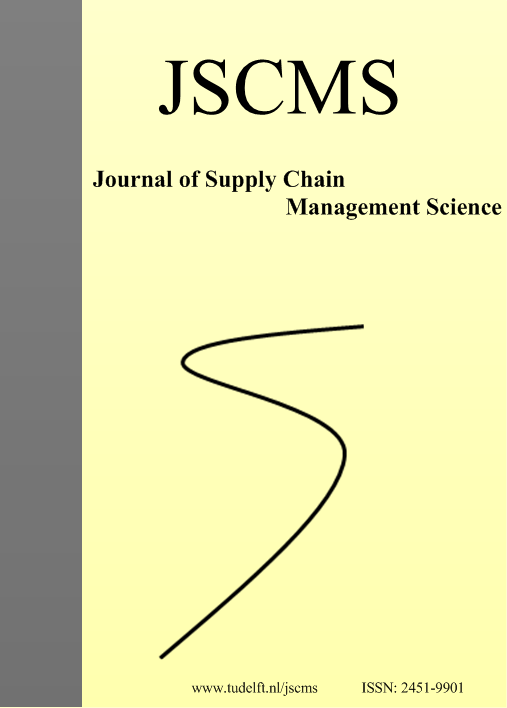
Several jobs can be found by browsing the federal government's website, USAJOBS. You can also search by degree type and title. While most of these jobs require at minimum a bachelor's degree in order to be eligible, some may require a masters. Supply chain specialists can also be found at smaller organizations. Supply chain professionals typically need to have at least one year of experience before they can apply.
There are many jobs for data scientists. Data Scientists support government programs and assist in the creation of strategic plans.
FAQ
What skills is required for a production planner?
Production planners must be flexible, organized, and able handle multiple tasks. You must also be able to communicate effectively with clients and colleagues.
What does it mean to be a manufacturer?
Manufacturing Industries refers to businesses that manufacture products. Consumers are the people who purchase these products. These companies employ many processes to achieve this purpose, such as production and distribution, retailing, management and so on. They manufacture goods from raw materials using machines and other equipment. This includes all types and varieties of manufactured goods, such as food items, clothings, building supplies, furnitures, toys, electronics tools, machinery vehicles, pharmaceuticals medical devices, chemicals, among others.
What does it mean to warehouse?
A warehouse is an area where goods are stored before being sold. It can be an outdoor or indoor area. In some cases it could be both indoors and outdoors.
Why automate your warehouse
Modern warehousing is becoming more automated. With the rise of ecommerce, there is a greater demand for faster delivery times as well as more efficient processes.
Warehouses should be able adapt quickly to new needs. To do so, they must invest heavily in technology. Automating warehouses is a great way to save money. These are some of the benefits that automation can bring to warehouses:
-
Increases throughput/productivity
-
Reduces errors
-
Increases accuracy
-
Safety is boosted
-
Eliminates bottlenecks
-
This allows companies to scale easily
-
It makes workers more efficient
-
Gives you visibility into all that is happening in your warehouse
-
Enhances customer experience
-
Improves employee satisfaction
-
It reduces downtime, and increases uptime
-
High quality products delivered on-time
-
Eliminates human error
-
This helps to ensure compliance with regulations
How important is automation in manufacturing?
Automating is not just important for manufacturers, but also for service providers. It enables them to provide services faster and more efficiently. They can also reduce their costs by reducing human error and improving productivity.
What is the role of a production manager?
Production planners make sure that every aspect of the project is delivered on-time, within budget, and within schedule. A production planner ensures that the service and product meet the client's expectations.
Statistics
- You can multiply the result by 100 to get the total percent of monthly overhead. (investopedia.com)
- According to a Statista study, U.S. businesses spent $1.63 trillion on logistics in 2019, moving goods from origin to end user through various supply chain network segments. (netsuite.com)
- According to the United Nations Industrial Development Organization (UNIDO), China is the top manufacturer worldwide by 2019 output, producing 28.7% of the total global manufacturing output, followed by the United States, Japan, Germany, and India.[52][53] (en.wikipedia.org)
- [54][55] These are the top 50 countries by the total value of manufacturing output in US dollars for its noted year according to World Bank.[56] (en.wikipedia.org)
- (2:04) MTO is a production technique wherein products are customized according to customer specifications, and production only starts after an order is received. (oracle.com)
External Links
How To
How to use Lean Manufacturing in the production of goods
Lean manufacturing (or lean manufacturing) is a style of management that aims to increase efficiency, reduce waste and improve performance through continuous improvement. It was developed in Japan between 1970 and 1980 by Taiichi Ohno. TPS founder Kanji Tyoda gave him the Toyota Production System, or TPS award. Michael L. Watkins published the original book on lean manufacturing, "The Machine That Changed the World," in 1990.
Lean manufacturing can be described as a set or principles that are used to improve quality, speed and cost of products or services. It emphasizes eliminating waste and defects throughout the value stream. Lean manufacturing is called just-in-time (JIT), zero defect, total productive maintenance (TPM), or 5S. Lean manufacturing eliminates non-value-added tasks like inspection, rework, waiting.
Lean manufacturing can help companies improve their product quality and reduce costs. Additionally, it helps them achieve their goals more quickly and reduces employee turnover. Lean manufacturing is a great way to manage the entire value chain including customers, suppliers, distributors and retailers as well as employees. Lean manufacturing practices are widespread in many industries. Toyota's philosophy, for example, is what has enabled it to be successful in electronics, automobiles, medical devices, healthcare and chemical engineering as well as paper and food.
Lean manufacturing includes five basic principles:
-
Define Value - Determine the value that your business brings to society. Also, identify what sets you apart from your competitors.
-
Reduce Waste – Eliminate all activities that don't add value throughout the supply chain.
-
Create Flow – Ensure that work flows smoothly throughout the process.
-
Standardize and Simplify – Make processes as consistent, repeatable, and as simple as possible.
-
Build Relationships - Establish personal relationships with both internal and external stakeholders.
Lean manufacturing, although not new, has seen renewed interest in the economic sector since 2008. Many businesses have adopted lean production techniques to make them more competitive. Economists think that lean manufacturing is a crucial factor in economic recovery.
Lean manufacturing is becoming a popular practice in automotive. It has many advantages. These include improved customer satisfaction, reduced inventory levels, lower operating costs, increased productivity, and better overall safety.
Any aspect of an enterprise can benefit from Lean manufacturing. Lean manufacturing is most useful in the production sector of an organisation because it ensures that each step in the value-chain is efficient and productive.
There are three types principally of lean manufacturing:
-
Just-in Time Manufacturing (JIT), also known as "pull system": This form of lean manufacturing is often referred to simply as "pull". JIT stands for a system where components are assembled on the spot rather than being made in advance. This approach aims to reduce lead times, increase the availability of parts, and reduce inventory.
-
Zero Defects Manufacturing (ZDM): ZDM focuses on ensuring that no defective units leave the manufacturing facility. If a part needs to be fixed during the assembly line, it should be repaired rather than scrapped. This applies to finished products, which may need minor repairs before they are shipped.
-
Continuous Improvement (CI: Continuous improvement aims to increase the efficiency of operations by constantly identifying and making improvements to reduce or eliminate waste. Continuous Improvement (CI) involves continuous improvement in processes, people, tools, and infrastructure.