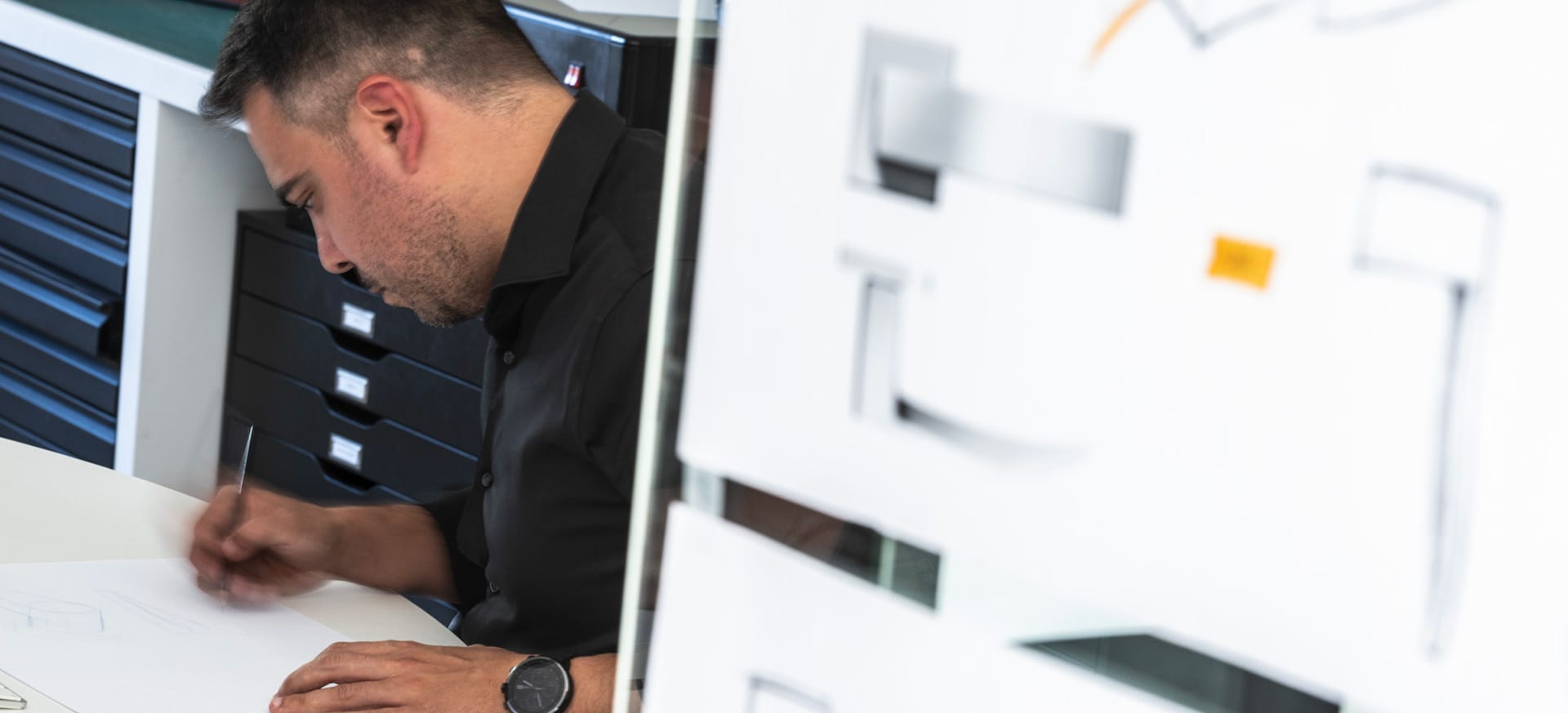
Despite the numerous benefits of lean manufacturing, a number of companies have faced challenges in implementing this strategy. It is crucial that companies create a comprehensive plan to overcome any obstacles. Companies that have used Lean have discovered that there are three major issues that can hinder the success of the initiative.
Whatever the company's size, it is essential that they are committed to lean manufacturing. There is no one way to tell if a company is committed to lean manufacturing, but it is crucial that the management educates employees about the changes in corporate culture.
It is also crucial to ensure that resources get allocated correctly. Public organizations often find that they spend their budgets on unnecessary items. According to some reports, managers also purchase equipment that's not necessary in order to maximize their budget. This can lead to operational bottlenecks and inefficient implementation of lean manufacturing.
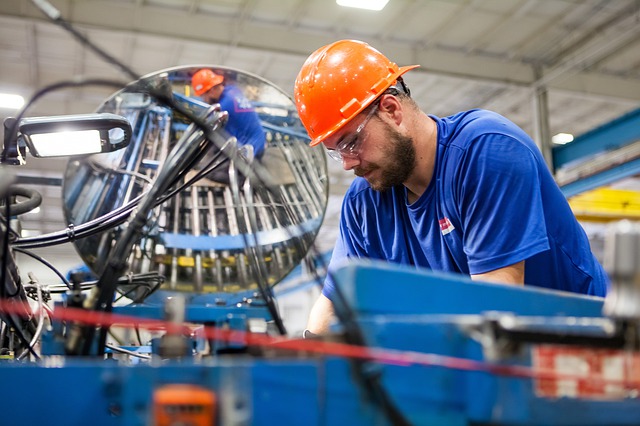
Resistance to cultural change is one of the greatest challenges when implementing lean manufacturing. Many employees are uncomfortable with change, particularly those who have been working in the company for a while. Some employees may wait to hear the majority's support before they make the change. Managers must share the benefits of their program and explain why it is necessary to overcome resistance.
Another problem is the absence of a comprehensive strategic transformation plan. Even though companies may be able to transform many business operations at once; it is vital that they have a long term strategy. Companies can use this strategy to mentor and identify future leaders, improve their operations, and ensure that they remain competitive in the face technological advances. It also helps identify and address operational bottlenecks and identify and address growth opportunities.
It is vital to train workers to overcome resistance. Training is essential to help workers understand their roles and expectations. Workers also learn multi-skills that they can use to be more independent. Additionally, training helps workers improve their problem solving skills which will help them to sustain Lean through improved performance.
Management should engage with workers regularly to overcome resistance. While managers may use pressure to get workers to comply with instructions, managers also need to take the time to explain why the change is necessary. Managers have been accused of giving incorrect instructions to employees, leading sometimes to ineffective implementation.
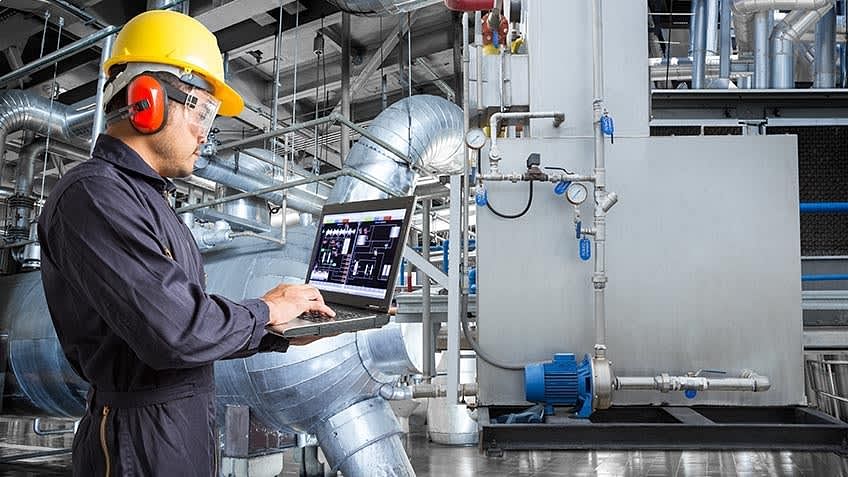
Managers, regardless of company size, must be present at the shop floor to help identify areas for improvement. They should also design and implement structured training programs for staff, as well as introduce digital tools to their work environment. These tools, such 5S, can improve visual management.
A clear vision is essential for lean manufacturing implementation. This vision should include the responsibilities for employees, a schedule and a method of measuring success.
FAQ
How can we improve manufacturing efficiency?
First, identify the factors that affect production time. Then we need to find ways to improve these factors. If you don't know where to start, then think about which factor(s) have the biggest impact on production time. Once you've identified them, try to find solutions for each of those factors.
What is it like to manage a logistics company?
A successful logistics business requires a lot more than just knowledge. You must have good communication skills to interact effectively with your clients and suppliers. You need to understand how to analyze data and draw conclusions from it. You will need to be able handle pressure well and work in stressful situations. To improve efficiency, you must be innovative and creative. You need to have strong leadership qualities to motivate team members and direct them towards achieving organizational goals.
You should also be organized and efficient to meet tight deadlines.
What does manufacturing industry mean?
Manufacturing Industries refers to businesses that manufacture products. Consumers are the people who purchase these products. This is accomplished by using a variety of processes, including production, distribution and retailing. They create goods from raw materials, using machines and various other equipment. This includes all types and varieties of manufactured goods, such as food items, clothings, building supplies, furnitures, toys, electronics tools, machinery vehicles, pharmaceuticals medical devices, chemicals, among others.
How can manufacturing reduce production bottlenecks?
To avoid production bottlenecks, ensure that all processes run smoothly from the moment you receive your order to the time the product ships.
This includes both quality control and capacity planning.
This can be done by using continuous improvement techniques, such as Six Sigma.
Six Sigma can be used to improve the quality and decrease waste in all areas of your company.
It seeks to eliminate variation and create consistency in your work.
Is there anything we should know about Manufacturing Processes prior to learning about Logistics.
No. You don't have to know about manufacturing processes before learning about logistics. However, knowing about manufacturing processes will definitely give you a better understanding of how logistics works.
Statistics
- Job #1 is delivering the ordered product according to specifications: color, size, brand, and quantity. (netsuite.com)
- [54][55] These are the top 50 countries by the total value of manufacturing output in US dollars for its noted year according to World Bank.[56] (en.wikipedia.org)
- You can multiply the result by 100 to get the total percent of monthly overhead. (investopedia.com)
- In 2021, an estimated 12.1 million Americans work in the manufacturing sector.6 (investopedia.com)
- It's estimated that 10.8% of the U.S. GDP in 2020 was contributed to manufacturing. (investopedia.com)
External Links
How To
How to Use lean manufacturing in the Production of Goods
Lean manufacturing is a management style that aims to increase efficiency and reduce waste through continuous improvement. It was developed in Japan between 1970 and 1980 by Taiichi Ohno. TPS founder Kanji Tyoda gave him the Toyota Production System, or TPS award. The first book published on lean manufacturing was titled "The Machine That Changed the World" written by Michael L. Watkins and published in 1990.
Lean manufacturing refers to a set of principles that improve the quality, speed and costs of products and services. It emphasizes the elimination of defects and waste throughout the value stream. Just-in-time (JIT), zero defect (TPM), and 5S are all examples of lean manufacturing. Lean manufacturing seeks to eliminate non-value added activities, such as inspection, work, waiting, and rework.
Lean manufacturing not only improves product quality but also reduces costs. Companies can also achieve their goals faster by reducing employee turnover. Lean Manufacturing is one of the most efficient ways to manage the entire value chains, including suppliers and customers as well distributors and retailers. Lean manufacturing practices are widespread in many industries. For example, Toyota's philosophy underpins its success in automobiles, electronics, appliances, healthcare, chemical engineering, aerospace, paper, food, etc.
Five basic principles of Lean Manufacturing are included in lean manufacturing
-
Define Value - Determine the value that your business brings to society. Also, identify what sets you apart from your competitors.
-
Reduce Waste – Eliminate all activities that don't add value throughout the supply chain.
-
Create Flow - Ensure work moves smoothly through the process without interruption.
-
Standardize and simplify – Make processes as repeatable and consistent as possible.
-
Build Relationships - Establish personal relationships with both internal and external stakeholders.
Although lean manufacturing has always been around, it is gaining popularity in recent years because of a renewed interest for the economy after 2008's global financial crisis. Many businesses have adopted lean manufacturing techniques to help them become more competitive. Many economists believe lean manufacturing will play a major role in economic recovery.
Lean manufacturing is becoming a popular practice in automotive. It has many advantages. These include higher customer satisfaction, lower inventory levels, lower operating expenses, greater productivity, and improved overall safety.
Lean manufacturing can be applied to almost every aspect of an organization. Lean manufacturing is most useful in the production sector of an organisation because it ensures that each step in the value-chain is efficient and productive.
There are three types of lean manufacturing.
-
Just-in Time Manufacturing, (JIT): This kind of lean manufacturing is also commonly known as "pull-systems." JIT stands for a system where components are assembled on the spot rather than being made in advance. This strategy aims to decrease lead times, increase availability of parts and reduce inventory.
-
Zero Defects Manufacturing (ZDM),: ZDM is a system that ensures no defective units are left the manufacturing facility. It is better to repair a part than have it removed from the production line if it needs to be fixed. This also applies to finished products that need minor repairs before being shipped.
-
Continuous Improvement (CI), also known as Continuous Improvement, aims at improving the efficiency of operations through continuous identification and improvement to minimize or eliminate waste. Continuous improvement involves continuous improvement of processes and people as well as tools.