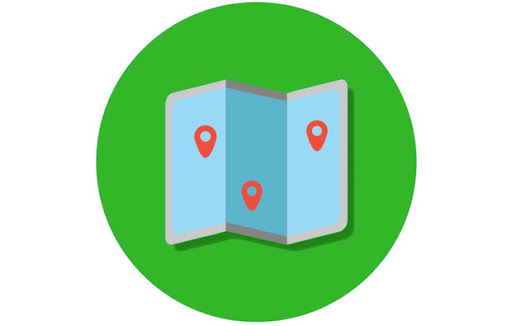
A supply chain management involves many aspects of a company. This includes both internal processes and the flow and distribution of finished goods and information. Supply chain management is also a component of marketing. Nearly every industry uses supply chains. The primary function of the supply chains is to deliver products to customers. It is common to deliver products on schedule.
An operations manager is responsible for managing business processes. This includes managing staff and equipment, as well as overseeing hiring. They also oversee production and planning. They are tasked with creating a strategy to improve operations. The operations manager also needs to make sure that there is enough inventory for production, that it is within the company's budget, and that it meets the specifications of the company. He works with the supply chain manager to ship orders directly to consumers and retailers.
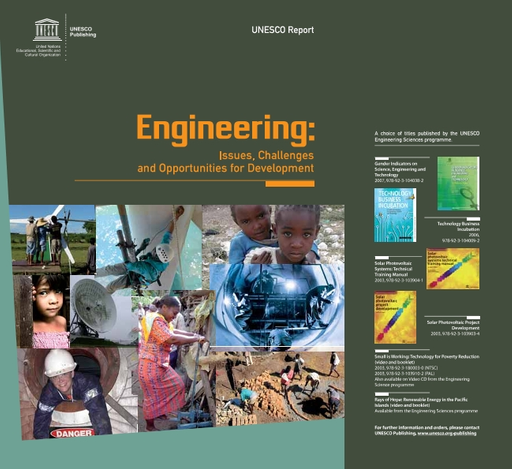
The operations and supply chains program at UTSA is designed for you to enhance your leadership and analytical skills. It's a hands-on program that combines classroom instruction with an experiential learning approach. The program offers data analysis skills, business process improvement, green belt certification in Lean Six Sigma, and Lean Six Sigma. The program gives an in-depth overview of operations and the supply chain industry. You will also have the opportunity to learn new technologies and apply them to your business.
The supply chain and operations program is focused on value-adding processes. The program gives students the tools they need to make smarter business decisions. This program is based on a range of industrial cases and case studies. The program teaches students how to communicate effectively and computer skills. This program also offers a minor. The minor complements the major and helps students maximize their supply chain effectiveness. The minor can also serve as a Contexts & Perspectives course and an unrestricted option.
Students have the opportunity to learn how to make better business decisions through the operations and supply chain program. The program also gives students the opportunity to apply concepts in their own business. It can also serve as a stepping stone to management, marketing, technology, and other career paths. You can also apply to the Lean Six Sigma green belt certificate. You can also interact with industry professionals and learn new technologies and trends.
The operations and supply chain program also provides opportunities for students to learn about the processes involved in the creation of products and services. It also teaches students the skills of communication, which are essential in business and managerial management.
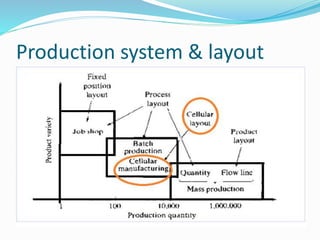
The book is written in a user-friendly style. It's appropriate for students of all backgrounds. In addition to describing how the supply chain works, the book presents a number of case studies, and discusses how to design a supply network. The book also explains quantitative methods for comparing demand and supply. It also explains how to incorporate customers into your supply chain.
FAQ
Can we automate some parts of manufacturing?
Yes! Yes! Automation has existed since ancient times. The Egyptians invented the wheel thousands of years ago. Nowadays, we use robots for assembly lines.
In fact, there are several applications of robotics in manufacturing today. These include:
-
Robots for assembly line
-
Robot welding
-
Robot painting
-
Robotics inspection
-
Robots that make products
Automation can be applied to manufacturing in many other ways. 3D printing makes it possible to produce custom products in a matter of days or weeks.
What skills should a production planner have?
Being a production planner is not easy. You need to be organized and flexible. It is also important to be able communicate with colleagues and clients.
What does manufacturing mean?
Manufacturing Industries are companies that manufacture products. These products are sold to consumers. To accomplish this goal, these companies employ a range of processes including distribution, sales, management, and production. They produce goods from raw materials by using machines and other machinery. This includes all types manufactured goods such as clothing, building materials, furniture, electronics, tools and machinery.
What do you mean by warehouse?
A warehouse, or storage facility, is where goods are stored prior to being sold. It can be an indoor space or an outdoor area. Sometimes, it can be both an indoor and outdoor space.
How can manufacturing reduce production bottlenecks?
Avoiding production bottlenecks is as simple as keeping all processes running smoothly, from the time an order is received until the product ships.
This includes both quality control and capacity planning.
Continuous improvement techniques like Six Sigma are the best way to achieve this.
Six Sigma can be used to improve the quality and decrease waste in all areas of your company.
It emphasizes consistency and eliminating variance in your work.
Statistics
- In 2021, an estimated 12.1 million Americans work in the manufacturing sector.6 (investopedia.com)
- According to a Statista study, U.S. businesses spent $1.63 trillion on logistics in 2019, moving goods from origin to end user through various supply chain network segments. (netsuite.com)
- Job #1 is delivering the ordered product according to specifications: color, size, brand, and quantity. (netsuite.com)
- According to the United Nations Industrial Development Organization (UNIDO), China is the top manufacturer worldwide by 2019 output, producing 28.7% of the total global manufacturing output, followed by the United States, Japan, Germany, and India.[52][53] (en.wikipedia.org)
- (2:04) MTO is a production technique wherein products are customized according to customer specifications, and production only starts after an order is received. (oracle.com)
External Links
How To
Six Sigma: How to Use it in Manufacturing
Six Sigma refers to "the application and control of statistical processes (SPC) techniques in order to achieve continuous improvement." Motorola's Quality Improvement Department developed it at their Tokyo plant in Japan in 1986. Six Sigma's main goal is to improve process quality by standardizing processes and eliminating defects. Many companies have adopted Six Sigma in recent years because they believe that there are no perfect products and services. Six Sigma aims to reduce variation in the production's mean value. This means that you can take a sample from your product and then compare its performance to the average to find out how often the process differs from the norm. If it is too large, it means that there are problems.
Understanding the nature of variability in your business is the first step to Six Sigma. Once you understand that, it is time to identify the sources of variation. You'll also want to determine whether these variations are random or systematic. Random variations occur when people make mistakes; systematic ones are caused by factors outside the process itself. Random variations would include, for example, the failure of some widgets to fall from the assembly line. You might notice that your widgets always fall apart at the same place every time you put them together.
Once you have identified the problem, you can design solutions. The solution could involve changing how you do things, or redesigning your entire process. You should then test the changes again after they have been implemented. If they don’t work, you’ll need to go back and rework the plan.