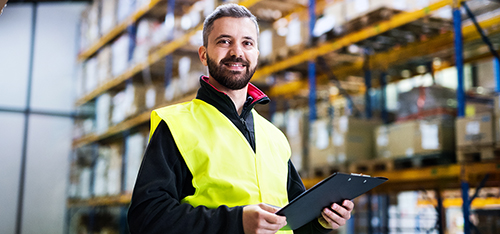
Industrial Engineering Managers can be crucial members of any team. They are responsible for directing staff and improving production output. This includes managing the factory floor's layout and design, and overseeing implementation of processes and procedures. Aside from their technical expertise, they can help companies develop new products or processes.
They are responsible in developing and maintaining effective manufacturing processes. This requires an in-depth knowledge of current trends in automation, robotics, and other related technologies. They need to ensure safety and health compliance, as well as monitor and maintain industrial operations. They are responsible for ensuring that raw materials and consumables are used properly. They also conduct space and workflow studies. They oversee the execution of all work projects. This includes cycle time reduction, product costs reduction and process improvement. They also manage preventative maintenance.
The manager works in collaboration with other teams to develop new processes, improve efficiency, and streamline operations. He or she is also responsible for the design and installation, as well as renovations to facilities. Managers communicate technical information to non-technical parties as part of the project management process. Managers also ensure that resources are available for their teams. They also visit suppliers' facilities. He or she represents the team members and ensures compliance with quality guidelines.
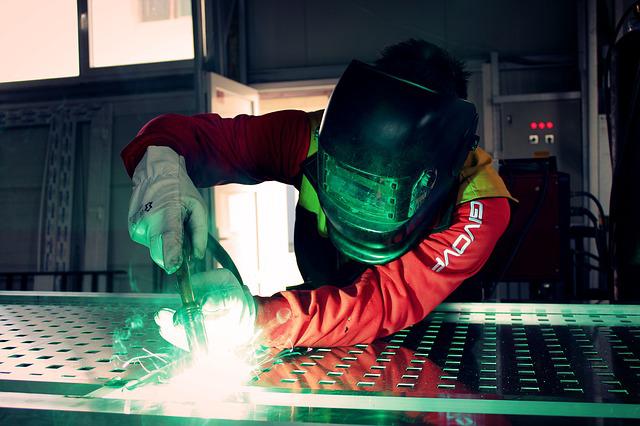
Industrial Engineering Managers are expected to be highly motivated, creative, and able to solve problems. They must be able to work in hot and cold environments, be physically fit, and climb and walk for 8 to 12 hours a day. Aside from that, they need to be able and able to communicate well with all levels.
Industrial engineering managers must hold a degree in engineering, or a related field. They must also have at minimum five years of relevant experience. Employers prefer candidates who have completed postgraduate studies. These candidates may also require specific skills such as project management and logistics.
Industrial Engineering Managers are responsible for the development and creation of new products. They have a strong background in problem-solving and quality improvement. They are also able to work in a team setting. Managers are more successful when they are able to encourage employee growth.
Industrial Engineers have the ability to streamline operations and reduce costs. They are knowledgeable in manufacturing processes, and enjoy meeting deadlines. They are also familiar with human resources, logistics, recruiting, vendor and supplier relations, as well as recruitment. They are skilled in setting goals, managing procedures, and creating budgets. They are also able to prepare strategies to increase the efficiency of engineering projects.
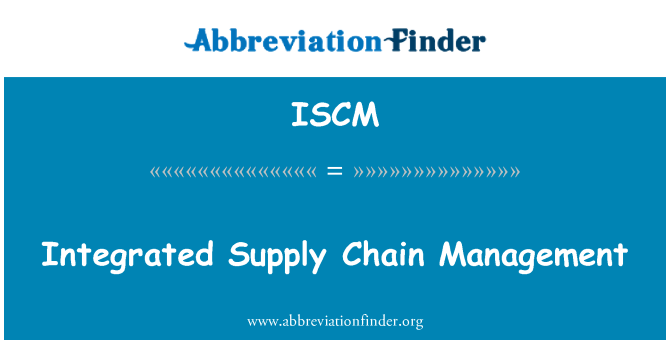
The industrial engineering manager may be responsible for the design and execution of new manufacturing procedures or operating equipment. They will need to develop plans and operate methods that conform to existing standards and guidelines. They are responsible for overseeing the implementation of waste elimination plans. They also have to analyze the factory's labor productivity.
Industrial Engineering Managers have the ability to contribute their knowledge in creating strategies for improving productivity, developing products, and managing people resources. They can also aid in the development and improvement of existing processes.
FAQ
Why is logistics important for manufacturing?
Logistics are an integral part any business. They enable you to achieve outstanding results by helping manage product flow from raw materials through to finished goods.
Logistics play an important role in reducing costs as well as increasing efficiency.
What is the role of a production manager?
A production planner ensures all aspects of the project are delivered on time, within budget, and within scope. They make sure that the product and services meet client expectations.
Why automate your factory?
Modern warehouses have become more dependent on automation. With the rise of ecommerce, there is a greater demand for faster delivery times as well as more efficient processes.
Warehouses must adapt quickly to meet changing customer needs. Technology is essential for warehouses to be able to adapt quickly to changing needs. Automation of warehouses offers many benefits. Here are some of the reasons automation is worth your investment:
-
Increases throughput/productivity
-
Reduces errors
-
Improves accuracy
-
Boosts safety
-
Eliminates bottlenecks
-
Companies can scale up more easily
-
Workers are more productive
-
Provides visibility into everything that happens in the warehouse
-
Enhances customer experience
-
Improves employee satisfaction
-
Reducing downtime and increasing uptime
-
This ensures that quality products are delivered promptly
-
Removing human error
-
Helps ensure compliance with regulations
Statistics
- You can multiply the result by 100 to get the total percent of monthly overhead. (investopedia.com)
- (2:04) MTO is a production technique wherein products are customized according to customer specifications, and production only starts after an order is received. (oracle.com)
- Many factories witnessed a 30% increase in output due to the shift to electric motors. (en.wikipedia.org)
- According to the United Nations Industrial Development Organization (UNIDO), China is the top manufacturer worldwide by 2019 output, producing 28.7% of the total global manufacturing output, followed by the United States, Japan, Germany, and India.[52][53] (en.wikipedia.org)
- It's estimated that 10.8% of the U.S. GDP in 2020 was contributed to manufacturing. (investopedia.com)
External Links
How To
How to Use lean manufacturing in the Production of Goods
Lean manufacturing refers to a method of managing that seeks to improve efficiency and decrease waste. It was developed by Taiichi Okono in Japan, during the 1970s & 1980s. TPS founder Kanji Takoda awarded him the Toyota Production System Award (TPS). Michael L. Watkins published the book "The Machine That Changed the World", which was the first to be published about lean manufacturing.
Lean manufacturing, often described as a set and practice of principles, is aimed at improving the quality, speed, cost, and efficiency of products, services, and other activities. It emphasizes the elimination of defects and waste throughout the value stream. Lean manufacturing is also known as just in time (JIT), zero defect total productive maintenance(TPM), and five-star (S). Lean manufacturing focuses on eliminating non-value-added activities such as rework, inspection, and waiting.
Lean manufacturing improves product quality and costs. It also helps companies reach their goals quicker and decreases employee turnover. Lean manufacturing has been deemed one of the best ways to manage the entire value-chain, including customers, distributors as well retailers and employees. Lean manufacturing is widely used in many industries. Toyota's philosophy has been a key driver of success in many industries, including automobiles and electronics.
Lean manufacturing is based on five principles:
-
Define value - Find out what your business contributes to society, and what makes it different from other competitors.
-
Reduce waste - Stop any activity that isn't adding value to the supply chains.
-
Create Flow. Ensure that your work is uninterrupted and flows seamlessly.
-
Standardize and simplify - Make your processes as consistent as possible.
-
Develop Relationships: Establish personal relationships both with internal and external stakeholders.
Lean manufacturing isn’t new, but it has seen a renewed interest since 2008 due to the global financial crisis. Many companies have adopted lean manufacturing methods to increase their marketability. Many economists believe lean manufacturing will play a major role in economic recovery.
Lean manufacturing has many benefits in the automotive sector. These benefits include increased customer satisfaction, reduced inventory levels and lower operating costs.
You can apply Lean Manufacturing to virtually any aspect of your organization. It is especially useful for the production aspect of an organization, as it ensures that every step in the value chain is efficient and effective.
There are three types principally of lean manufacturing:
-
Just-in Time Manufacturing (JIT), also known as "pull system": This form of lean manufacturing is often referred to simply as "pull". JIT is a process in which components can be assembled at the point they are needed, instead of being made ahead of time. This strategy aims to decrease lead times, increase availability of parts and reduce inventory.
-
Zero Defects Manufacturing (ZDM): ZDM focuses on ensuring that no defective units leave the manufacturing facility. Repairing a part that is damaged during assembly should be done, not scrapping. This applies to finished goods that may require minor repairs before shipment.
-
Continuous Improvement (CI), also known as Continuous Improvement, aims at improving the efficiency of operations through continuous identification and improvement to minimize or eliminate waste. Continuous improvement refers to continuous improvement of processes as well people and tools.