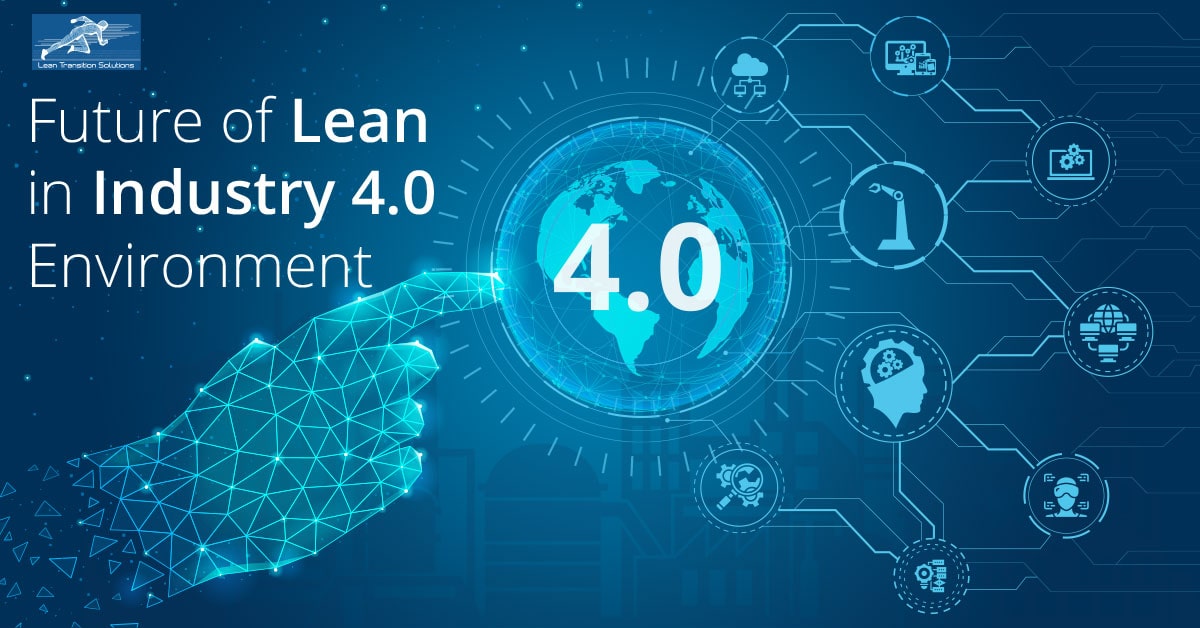
You need to consider manufacturing cost when making sure you produce a product that is financially viable. You may need to buy wood, adhesives and other materials if your plan is to sell wooden tabletop furnishings. So that your finished product is durable, it is important to source the best raw material from reliable suppliers. If you don't choose high-quality materials, your product could break and you may lose revenue.
The best way to determine manufacturing cost is to break it up into three main categories. Each of these costs will have an effect on the final cost of the product you are selling. The unit cost, which represents the cost of producing an item, is one of the most important elements of a manufacturing cost. This number is a good way to begin, but it is not easy to determine.
A good rule of thumb when trying to determine the most cost-effective manufacturing option for your company is the units per hour or unit/unit ratio. To illustrate, let's say you want to make 5,000 wooden table tops. You can find the average cost by subtracting the amount of time required to complete the project.
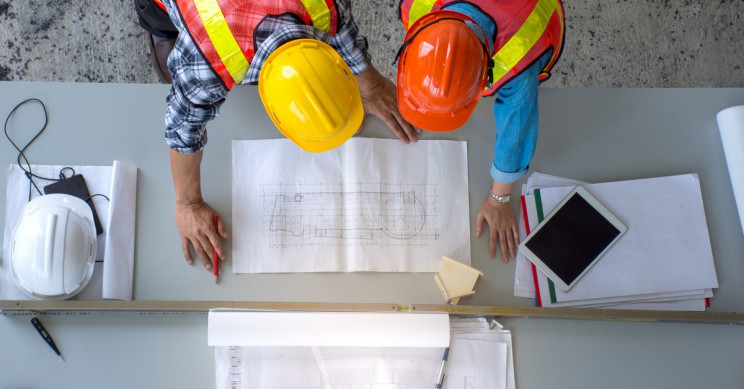
Apart from direct labor and production equipment, budgeting will also be necessary for administrative and other general expenses. These include advertising costs, office supplies rent, and commissions. Compliance with regulatory requirements will require you to spend substantial amounts. Online inventory control software can be used to track and forecast production.
Direct labor costs include wages paid to factory workers and employees involved in the preparation of goods for manufacturing. These costs may include staff such as maintenance, sanitation, and bookkeepers. In general, the hourly wage for direct labor is around $150.
Manufacturing has indirect costs. These include utility bills and maintenance costs. You will need to determine the costs of the preparation and assembly of the materials, as well as the costs to deliver the product to the customer. You can calculate the cost of manufacturing and get an estimate of the overhead costs for the following fiscal year by creating a manufacturing overhead account.
When calculating manufacturing costs, you should also consider the indirect and direct materials that were used in the manufacture of the product. The materials used to manufacture a product include thread, wood, and cotton. A poor quality product can lead to inferior results. You will also need to test the safety of your products if you are a food processor in certain areas.
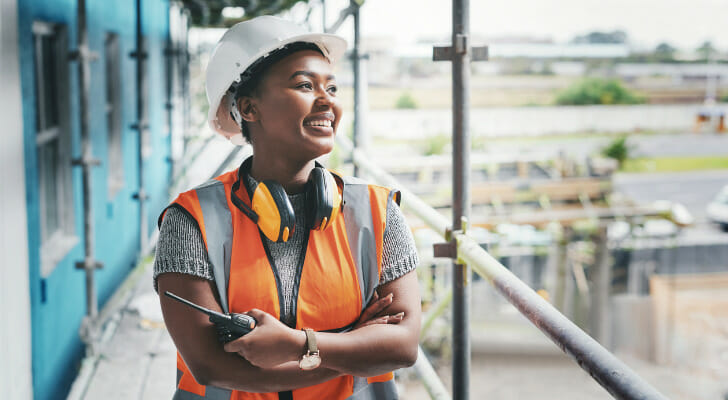
You can determine whether to start manufacturing a new product by knowing the unit-per-unit cost and the manufacturing cost. It is also important to determine the pricing of your products in order to increase your company's profitability.
FAQ
What does it mean to be a manufacturer?
Manufacturing Industries are businesses that produce products for sale. These products are sold to consumers. These companies use various processes such as production, distribution, retailing, management, etc., to fulfill this purpose. They create goods from raw materials, using machines and various other equipment. This includes all types and varieties of manufactured goods, such as food items, clothings, building supplies, furnitures, toys, electronics tools, machinery vehicles, pharmaceuticals medical devices, chemicals, among others.
What can I do to learn more about manufacturing?
Hands-on experience is the best way to learn more about manufacturing. You can read books, or watch instructional videos if you don't have the opportunity to do so.
Why is logistics important in manufacturing?
Logistics are an essential component of any business. They enable you to achieve outstanding results by helping manage product flow from raw materials through to finished goods.
Logistics plays a significant role in reducing cost and increasing efficiency.
Can some manufacturing processes be automated?
Yes! Yes. The Egyptians created the wheel thousands years ago. Today, robots assist in the assembly of lines.
In fact, there are several applications of robotics in manufacturing today. These include:
-
Automated assembly line robots
-
Robot welding
-
Robot painting
-
Robotics inspection
-
Robots that create products
Manufacturing could also benefit from automation in other ways. 3D printing is a way to make custom products quickly and without waiting weeks or months for them to be manufactured.
What are the jobs in logistics?
There are many jobs available in logistics. Here are some:
-
Warehouse workers - They load trucks and pallets.
-
Transport drivers - These are people who drive trucks and trailers to transport goods or perform pick-ups.
-
Freight handlers are people who sort and pack freight into warehouses.
-
Inventory managers: They are responsible for the inventory and management of warehouses.
-
Sales representatives - They sell products to customers.
-
Logistics coordinators - They plan and organize logistics operations.
-
Purchasing agents - They buy goods and services that are necessary for company operations.
-
Customer service representatives - They answer calls and emails from customers.
-
Ship clerks - They issue bills and process shipping orders.
-
Order fillers - They fill orders based on what is ordered and shipped.
-
Quality control inspectors (QCI) - They inspect all incoming and departing products for potential defects.
-
Others - There are many other types of jobs available in logistics, such as transportation supervisors, cargo specialists, etc.
What are the responsibilities of a logistic manager?
A logistics manager ensures that all goods are delivered on time and without damage. This is done through his/her expertise and knowledge about the company's product range. He/she should make sure that enough stock is on hand to meet the demands.
What are the requirements to start a logistics business?
It takes a lot of skills and knowledge to run a successful logistics business. You must have good communication skills to interact effectively with your clients and suppliers. You need to understand how to analyze data and draw conclusions from it. You must be able and able to handle stress situations and work under pressure. To improve efficiency, you must be innovative and creative. Strong leadership qualities are essential to motivate your team and help them achieve their organizational goals.
You should also be organized and efficient to meet tight deadlines.
Statistics
- (2:04) MTO is a production technique wherein products are customized according to customer specifications, and production only starts after an order is received. (oracle.com)
- According to a Statista study, U.S. businesses spent $1.63 trillion on logistics in 2019, moving goods from origin to end user through various supply chain network segments. (netsuite.com)
- According to the United Nations Industrial Development Organization (UNIDO), China is the top manufacturer worldwide by 2019 output, producing 28.7% of the total global manufacturing output, followed by the United States, Japan, Germany, and India.[52][53] (en.wikipedia.org)
- You can multiply the result by 100 to get the total percent of monthly overhead. (investopedia.com)
- In the United States, for example, manufacturing makes up 15% of the economic output. (twi-global.com)
External Links
How To
Six Sigma in Manufacturing:
Six Sigma is defined by "the application SPC (statistical process control) techniques to achieve continuous improvements." Motorola's Quality Improvement Department developed it at their Tokyo plant in Japan in 1986. Six Sigma's main goal is to improve process quality by standardizing processes and eliminating defects. Since there are no perfect products, or services, this approach has been adopted by many companies over the years. Six Sigma aims to reduce variation in the production's mean value. This means that you can take a sample from your product and then compare its performance to the average to find out how often the process differs from the norm. If you notice a large deviation, then it is time to fix it.
Understanding the dynamics of variability within your business is the first step in Six Sigma. Once you understand that, it is time to identify the sources of variation. This will allow you to decide if these variations are random and systematic. Random variations occur when people do mistakes. Symmetrical variations are caused due to factors beyond the process. Random variations would include, for example, the failure of some widgets to fall from the assembly line. If however, you notice that each time you assemble a widget it falls apart in exactly the same spot, that is a problem.
After identifying the problem areas, you will need to devise solutions. It might mean changing the way you do business or redesigning it entirely. You should then test the changes again after they have been implemented. If they fail, you can go back to the drawing board to come up with a different plan.