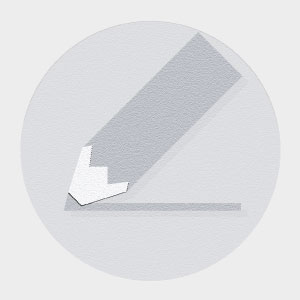
Oracle Supply Chain Management (OSCM) is a comprehensive solution that allows organizations to quickly adapt to changing conditions, create resilient networks, and improve forecast accuracy. With end-to-end visibility of the entire supply chain, Oracle SCM provides flexible supply chain planning that improves collaboration and minimizes costs. Oracle Fusion Cloud CMS allows you to streamline your business and collaborate with your suppliers more effectively. Oracle SCM helps you achieve these goals. You can also reduce disruptions, lower costs, and improve forecast accuracy.
Interface that is user-friendly
Several of the improvements in Oracle SCM are related to the user-friendly interface. This release makes the system easier to use and more accessible. A product based analyzer script provides recommendations, solutions, and early warnings. This is an excellent example. It is designed for identifying inbound transaction problems and providing solutions. It is also customizable.
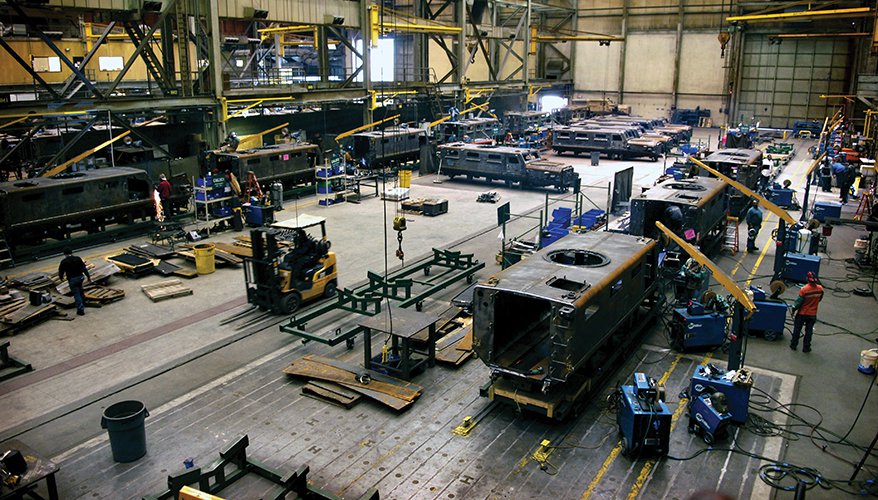
Cost management
Oracle SCM can help you define cost management policies and make decisions at the item-level. Cost profiles can be created by product or manufacturing process, and not just rely on one costing methodology. For instance, manufactured items may be driven by a standard rolled up cost, while repair items will use the actual costing method. The software supports both open and closed periods. The software also has cost simulation and copying capabilities.
Decision support
Oracle SCM provides decision support. This is the use of advanced analysis to improve the performance and efficiency of management processes. A comprehensive collection of business intelligence software tools allows management to make informed decisions based upon data and information. Oracle Strategic Enterprise Management applications are designed to support the strategic management techniques used by many organizations. Executives can use this technology to control costs and measure progress against a set plan. Employee performance can be measured and compensated. These applications can be integrated with Oracle's ERP systems and used as enterprise-wide solutions.
Compliance with the regulations
As regulations and laws continue to grow in number, so do the requirements for organizations to have effective ways of managing them. Oracle has the solution. Oracle SCM regulatory compliance solutions make it easier for organizations to meet their legal compliance and regulatory compliance requirements. The Oracle Cloud Platform offers flexible deployment options that can be used by organizations of any size. Oracle offers many configurable and customizable products that allow customers to stay compliant with regulations.
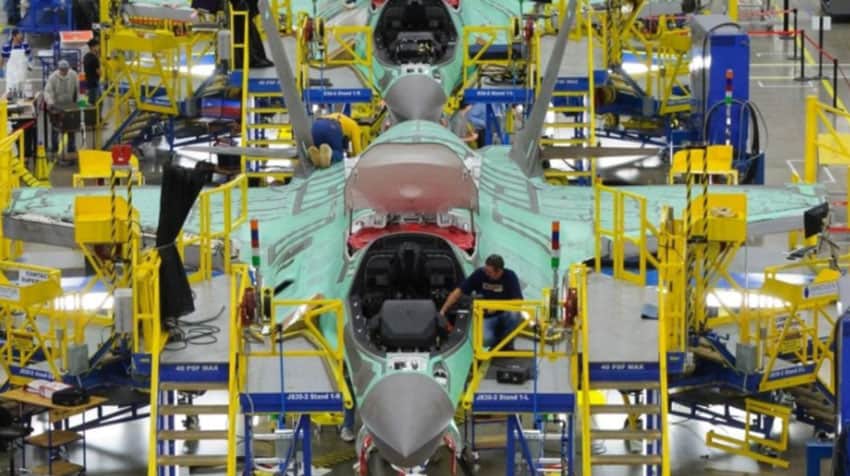
Flexible solution
Intellinum Inc., the world's leading supplier of supply chain mobility systems, created Flexi LogiPro. A flexible solution for Oracle SCM or Oracle WMSCloud, Flexi LogiPro is an innovative solution. This flexible mobile solution offers a mobile-friendly, customizable user interface that can be barcode enabled. It is compatible with Oracle SCM and WMSCloud and integrates with the backend systems in real-time. It's available in both cloud and on-premise deployments and allows companies the ability to tailor their mobile apps to their particular needs.
FAQ
What is the difference between manufacturing and logistics
Manufacturing refers the process of producing goods from raw materials through machines and processes. Logistics covers all aspects involved in managing supply chains, including procurement and production planning. Sometimes manufacturing and logistics are combined to refer to a wider term that includes both the process of creating products as well as their delivery to customers.
What is the difference between Production Planning and Scheduling?
Production Planning (PP), also known as forecasting and identifying production capacities, is the process that determines what product needs to be produced at any particular time. This is accomplished by forecasting the demand and identifying production resources.
Scheduling is the process of assigning specific dates to tasks so they can be completed within the specified timeframe.
What is meant by manufacturing industries?
Manufacturing Industries is a group of businesses that produce goods for sale. These products are sold to consumers. These companies use various processes such as production, distribution, retailing, management, etc., to fulfill this purpose. They make goods from raw materials with machines and other equipment. This includes all types of manufactured goods, including food items, clothing, building supplies, furniture, toys, electronics, tools, machinery, vehicles, pharmaceuticals, medical devices, chemicals, and many others.
Statistics
- According to a Statista study, U.S. businesses spent $1.63 trillion on logistics in 2019, moving goods from origin to end user through various supply chain network segments. (netsuite.com)
- Job #1 is delivering the ordered product according to specifications: color, size, brand, and quantity. (netsuite.com)
- You can multiply the result by 100 to get the total percent of monthly overhead. (investopedia.com)
- (2:04) MTO is a production technique wherein products are customized according to customer specifications, and production only starts after an order is received. (oracle.com)
- According to the United Nations Industrial Development Organization (UNIDO), China is the top manufacturer worldwide by 2019 output, producing 28.7% of the total global manufacturing output, followed by the United States, Japan, Germany, and India.[52][53] (en.wikipedia.org)
External Links
How To
How to Use Six Sigma in Manufacturing
Six Sigma refers to "the application and control of statistical processes (SPC) techniques in order to achieve continuous improvement." Motorola's Quality Improvement Department, Tokyo, Japan, developed it in 1986. Six Sigma is a method to improve quality through standardization and elimination of defects. Since there are no perfect products, or services, this approach has been adopted by many companies over the years. Six Sigma's primary goal is to reduce variation from the average value of production. It is possible to measure the performance of your product against an average and find the percentage of time that it differs from the norm. If you notice a large deviation, then it is time to fix it.
Understanding how your business' variability is a key step towards Six Sigma implementation is the first. Once you understand that, it is time to identify the sources of variation. You'll also want to determine whether these variations are random or systematic. Random variations occur when people do mistakes. Symmetrical variations are caused due to factors beyond the process. For example, if you're making widgets, and some of them fall off the assembly line, those would be considered random variations. If however, you notice that each time you assemble a widget it falls apart in exactly the same spot, that is a problem.
After identifying the problem areas, you will need to devise solutions. This could mean changing your approach or redesigning the entire process. Test them again once you've implemented the changes. If they didn't work, then you'll need to go back to the drawing board and come up with another plan.