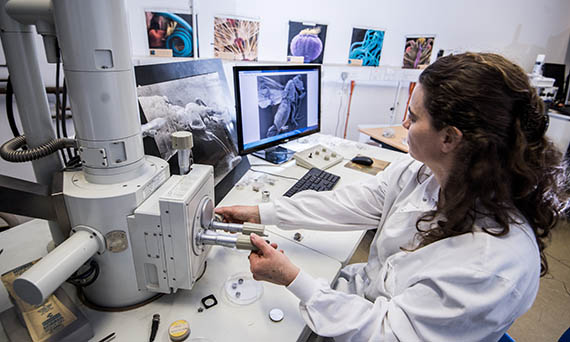
The food manufacturing industry employs many professionals and managers. Top executives decide policy and organize production operations. Industrial production managers oversee the day-today operations of a manufacturing factory. Managers of marketing, promotion, sales and community relations direct sales and marketing programs.
Food manufacturing jobs
Many food manufacturing jobs are available in New York. These three occupations are: food batchmakers, bakers, and packaging and filling machines operators. These occupations make up just about half of all food manufacturing jobs in the state. The state saw an increase in food manufacturing employment in seven of its 10 labor market areas.
There has been an improvement in the job market, which coincides well with the rise in food manufacturing jobs. In February, there was a 3.8% unemployment rate, the lowest point in more than ten years. Nondurable goods industries saw the largest increase in employment in food manufacturing, with 16,000 additional workers.
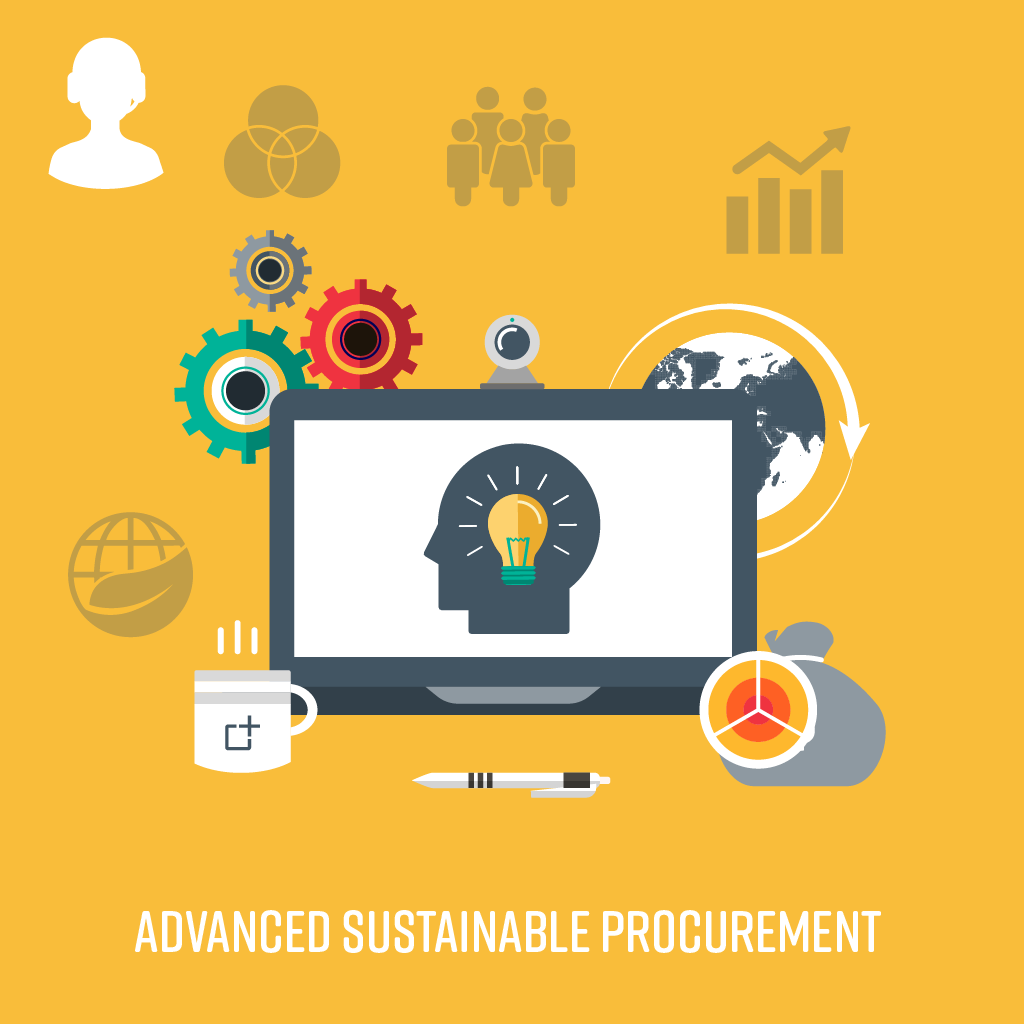
Average wages for workers in the industry
The average wage for workers in food production is between $26,000 and $52,000 per a year. The highest paid earn an average $52,000 per a year. Higher salaries are earned by those who have more experience. However, the lowest 10% earn less than $26,000 annually. Food Factory Workers' salaries are not as high as other jobs in the manufacturing sector, but they are generally within the same range.
Over the past few decades, average wages in this industry increased. The manufacturing industry is an integral part of our economy. However, it's not an isolated industry. Knowing how workers interact with other sectors of our economy is vital.
Localities with the greatest number of workers
2013 saw the concentration of food manufacturing businesses in three New York State labor marketplace regions: the Finger Lakes Region, the Southern Tier, or Western New York. These three regions combined employ almost half of all food manufacturing workers. These areas had high levels of food production, with the highest wages in the Hudson Valley, Southern Tier and Western New York.
Food processing is an industry that requires skilled labor. The lack of workers in some areas means that food manufacturing companies struggle to find workers with the proper skills. It's becoming more difficult to fill senior positions and to find workers for distribution trucks. Career site CareersInFood.com reports that food manufacturing job openings have increased by 12% in the last year. There has been a 37% increase in the 24 months.
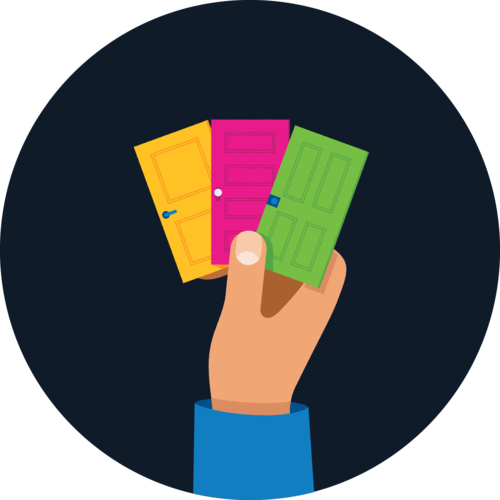
In the industry: The number of workers
According to the Bureau of Labor Statistics, the number of workers in the food manufacturing industry increased by 7.200 in February, a growth of over 1% from January. This month is the third consecutive month of job growth for this sector, which is slowly recovering after several headwinds. The industry's employment has been affected by the COVID-19 pandemic and a labor shortage. According to the Bureau of Labor Statistics in February, 40,700 people worked in the industry.
New York State's number of food processing firms grew by 8.8% between 2003-2013. Employment increased in four of the 10 labor market regions, with the largest increases in the Southern Tier and Hudson Valley.
FAQ
How can overproduction in manufacturing be reduced?
It is essential to find better ways to manage inventory to reduce overproduction. This would reduce the time needed to manage inventory. By doing this, we could free up resources for other productive tasks.
A Kanban system is one way to achieve this. A Kanban board can be used to monitor work progress. Kanban systems are where work items travel through a series of states until reaching their final destination. Each state represents a different priority.
As an example, if work is progressing from one stage of the process to another, then the current task is complete and can be transferred to the next. If a task is still in its beginning stages, it will continue to be so until it reaches the end.
This allows work to move forward and ensures that no work is missed. Managers can view the Kanban board to see how much work they have done. This information allows managers to adjust their workflow based off real-time data.
Lean manufacturing is another way to manage inventory levels. Lean manufacturing works to eliminate waste throughout every stage of the production chain. Waste includes anything that does not add value to the product. The following are examples of common waste types:
-
Overproduction
-
Inventory
-
Unnecessary packaging
-
Exceed materials
By implementing these ideas, manufacturers can improve efficiency and cut costs.
What is the importance of automation in manufacturing?
Automation is essential for both manufacturers and service providers. It allows them to offer services faster and more efficiently. They can also reduce their costs by reducing human error and improving productivity.
What is the difference between manufacturing and logistics
Manufacturing refers to the process of making goods using raw materials and machines. Logistics is the management of all aspects of supply chain activities, including procurement, production planning, distribution, warehousing, inventory control, transportation, and customer service. Manufacturing and logistics can often be grouped together to describe a larger term that covers both the creation of products, and the delivery of them to customers.
What does it take to run a logistics business?
To run a successful logistics company, you need a lot knowledge and skills. Good communication skills are essential to effectively communicate with your suppliers and clients. You must be able analyze data and draw out conclusions. You will need to be able handle pressure well and work in stressful situations. In order to innovate and create new ways to improve efficiency, creativity is essential. To motivate and guide your team towards reaching organizational goals, you must have strong leadership skills.
You must be organized to meet tight deadlines.
What is production planning?
Production Planning is the creation of a plan to cover all aspects, such as scheduling, budgeting. Location, crew, equipment, props and other details. This document ensures that everything is prepared and available when you are ready for shooting. This document should include information about how to achieve the best results on-set. This information includes locations, crew details and equipment requirements.
It is important to first outline the type of film you would like to make. You may already know where you want the film to be shot, or perhaps you have specific locations and sets you wish to use. Once you have determined your scenes and locations, it is time to start figuring out the elements that you will need for each scene. For example, you might decide that you need a car but don't know exactly what model you want. In this case, you could start looking up cars online to find out what models are available and then narrow your choices by choosing between different makes and models.
Once you have found the right car, you can start thinking about extras. What about additional seating? Or maybe you just need someone to push the car around. Perhaps you would like to change the interior colour from black to white. These questions will help determine the look and feel you want for your car. Also, think about what kind of shots you would like to capture. Will you be filming close-ups or wide angles? Perhaps you want to show the engine or the steering wheel? This will allow you to determine the type of car you want.
Once you have all the information, you are ready to create a plan. A schedule will tell you when you need to start shooting and when you need to finish. You will need to know when you have to be there, what time you have to leave and when your return home. So everyone is clear about what they need to do. Hire extra staff by booking them ahead of time. It's not worth paying someone to show up if you haven't told him.
Your schedule will also have to be adjusted to reflect the number of days required to film. Some projects may only take a couple of days, while others could last for weeks. When creating your schedule, be aware of whether you need more shots per day. Multiple shots at the same location can increase costs and make it more difficult to complete. It is better to be cautious and take fewer shots than you risk losing money if you are not sure if multiple takes are necessary.
Budgeting is another important aspect of production planning. A realistic budget will help you work within your means. Keep in mind that you can always reduce your budget if you face unexpected difficulties. You shouldn't underestimate the amount you'll spend. If you underestimate the cost of something, you will have less money left after paying for other items.
Production planning is a complicated process. But once you understand how everything works together, it becomes much easier to plan future project.
What are the 7 Rs of logistics?
The acronym 7R's for Logistics stands to represent the seven basic principles in logistics management. It was developed and published by the International Association of Business Logisticians in 2004 as part of the "Seven Principles of Logistics Management".
The acronym is composed of the following letters.
-
Responsive - ensure all actions are legal and not harmful to others.
-
Reliable: Have faith in your ability or the ability to honor any promises made.
-
Be responsible - Use resources efficiently and avoid wasting them.
-
Realistic – Consider all aspects, including cost-effectiveness as well as environmental impact.
-
Respectful - Treat people fairly and equitably
-
You are resourceful and look for ways to save money while increasing productivity.
-
Recognizable is a company that provides customers with value-added solutions.
How does a Production Planner differ from a Project Manager?
The major difference between a Production Planner and a Project Manager is that a Project Manager is often the person responsible for organizing and planning the entire project. While a Production Planner is involved mainly in the planning stage,
Statistics
- According to a Statista study, U.S. businesses spent $1.63 trillion on logistics in 2019, moving goods from origin to end user through various supply chain network segments. (netsuite.com)
- (2:04) MTO is a production technique wherein products are customized according to customer specifications, and production only starts after an order is received. (oracle.com)
- According to the United Nations Industrial Development Organization (UNIDO), China is the top manufacturer worldwide by 2019 output, producing 28.7% of the total global manufacturing output, followed by the United States, Japan, Germany, and India.[52][53] (en.wikipedia.org)
- [54][55] These are the top 50 countries by the total value of manufacturing output in US dollars for its noted year according to World Bank.[56] (en.wikipedia.org)
- You can multiply the result by 100 to get the total percent of monthly overhead. (investopedia.com)
External Links
How To
How to use the Just-In Time Method in Production
Just-in time (JIT), is a process that reduces costs and increases efficiency in business operations. It is a process where you get the right amount of resources at the right moment when they are needed. This means that your only pay for the resources you actually use. Frederick Taylor first coined this term while working in the early 1900s as a foreman. After observing how workers were paid overtime for late work, he realized that overtime was a common practice. He decided that workers would be more productive if they had enough time to complete their work before they started to work.
JIT is an acronym that means you need to plan ahead so you don’t waste your money. Also, you should look at the whole project from start-to-finish and make sure you have the resources necessary to address any issues. If you anticipate that there might be problems, you'll have enough people and equipment to fix them. This will prevent you from spending extra money on unnecessary things.
There are many JIT methods.
-
Demand-driven: This JIT is where you place regular orders for the parts/materials that are needed for your project. This will allow for you to track the material that you have left after using it. It will also allow you to predict how long it takes to produce more.
-
Inventory-based: You stock materials in advance to make your projects easier. This allows one to predict how much they will sell.
-
Project-driven: This is an approach where you set aside enough funds to cover the cost of your project. When you know how much you need, you'll purchase the appropriate amount of materials.
-
Resource-based JIT: This is the most popular form of JIT. Here you can allocate certain resources based purely on demand. You might assign more people to help with orders if there are many. If you don't have many orders, you'll assign fewer people to handle the workload.
-
Cost-based: This is similar to resource-based, except that here you're not just concerned about how many people you have but how much each person costs.
-
Price-based pricing: This is similar in concept to cost-based but instead you look at how much each worker costs, it looks at the overall company's price.
-
Material-based: This approach is similar to cost-based. However, instead of looking at the total cost for the company, you look at how much you spend on average on raw materials.
-
Time-based JIT: This is another variant of resource-based JIT. Instead of worrying about how much each worker costs, you can focus on how long the project takes.
-
Quality-based JIT - This is another form of resource-based JIT. Instead of thinking about how much each employee costs or how long it takes to manufacture something, you think about how good the quality of your product is.
-
Value-based JIT: This is the latest form of JIT. In this scenario, you're not concerned about how products perform or whether customers expect them to meet their expectations. Instead, you focus on the added value that you provide to your market.
-
Stock-based: This inventory-based approach focuses on how many items are being produced at any one time. It is used when production goals are met while inventory is kept to a minimum.
-
Just-intime (JIT), planning is a combination JIT management and supply chain management. It refers to the process of scheduling the delivery of components as soon as they are ordered. It is essential because it reduces lead-times and increases throughput.